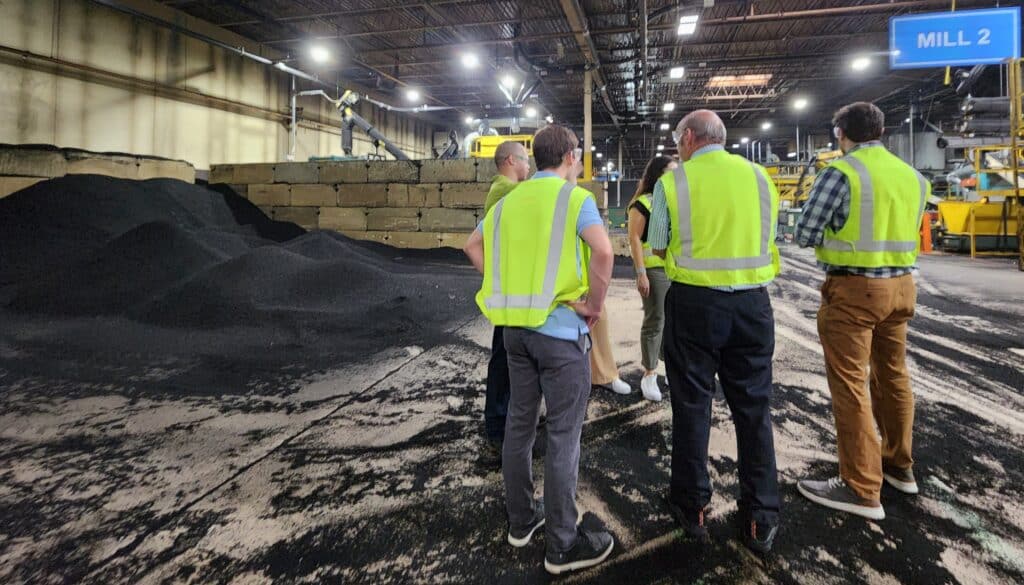
Let me tell you a COOL story where recycling meets innovation and quality products are made in the USA.
TeamPAR was graciously invited to visit the manufacturing facilities in York & Lancaster, PA for Ecore where they produce sport flooring & underlayment. They both recycle and produce in-house, and their custom capabilities are limitless. As designers who wear hardhats, TeamPAR was very impressed!
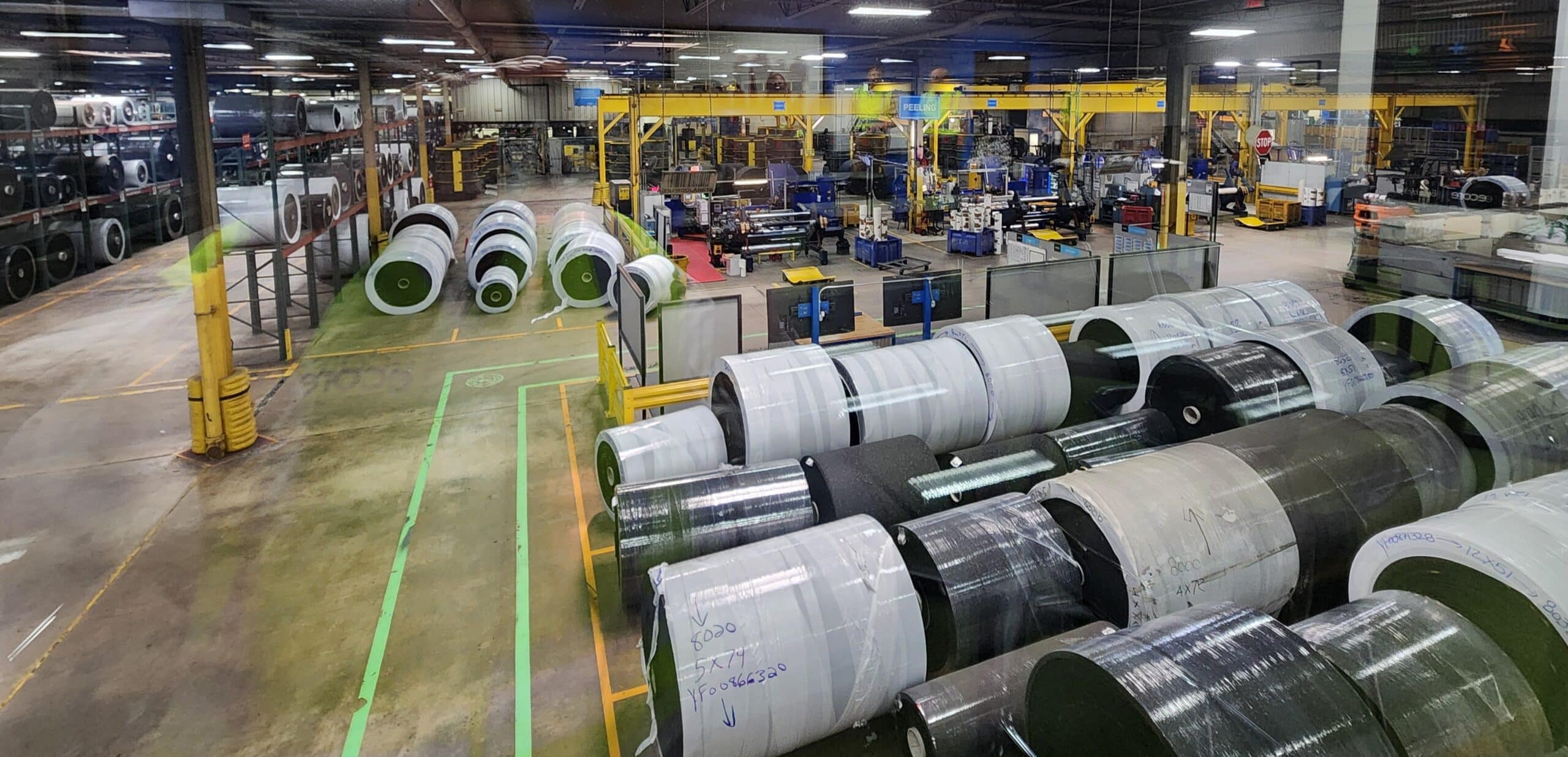
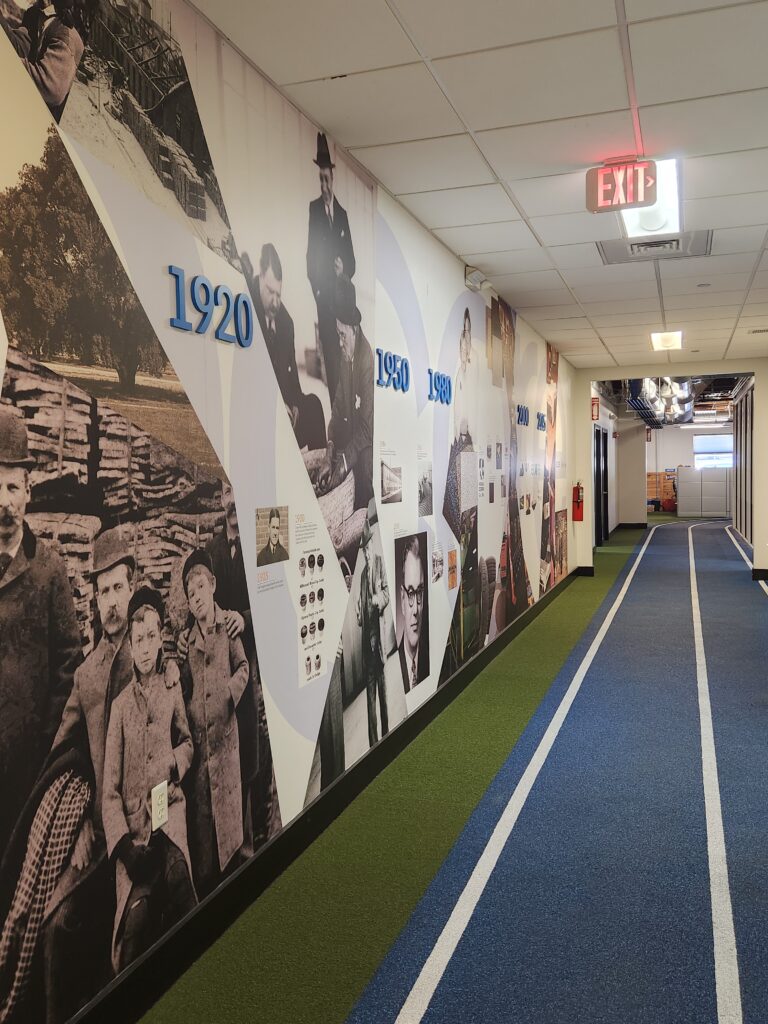
Did you know?
- That a roll of rubber (before it is turned into flooring) weighs between 3,500 – 10,000 pounds?
- 1,000 tires are recycled during every shift and 4,000 pounds of metal is removed every hour!
- Ecore has been in business since 1871! Ecore transforms reclaimed materials into performance surfaces that makes people’s lives better. https://www.ecoreintl.com/about-overview
Rich Willett, President of Flooring & Industrial, eloquently explained that the focus @ Ecore is circularity, upcycling, and people. To rid the world of waste is the purpose behind Ecore’s passion.
Flooring can be MORE than just flooring. Ecore’s products add value through ergonomics, safety and acoustics, bringing these attributes together in expert proportions.
Let me explain their process to you.
The recycling cycle (prequalification line) is comprised of 7 steps.
- Tire shredding
- Wire removal
- Granulated rubber process
- The mills (where contaminations are removed)
- Gravity separator (where stone and debris are removed)
- Screen line
- Material bagging
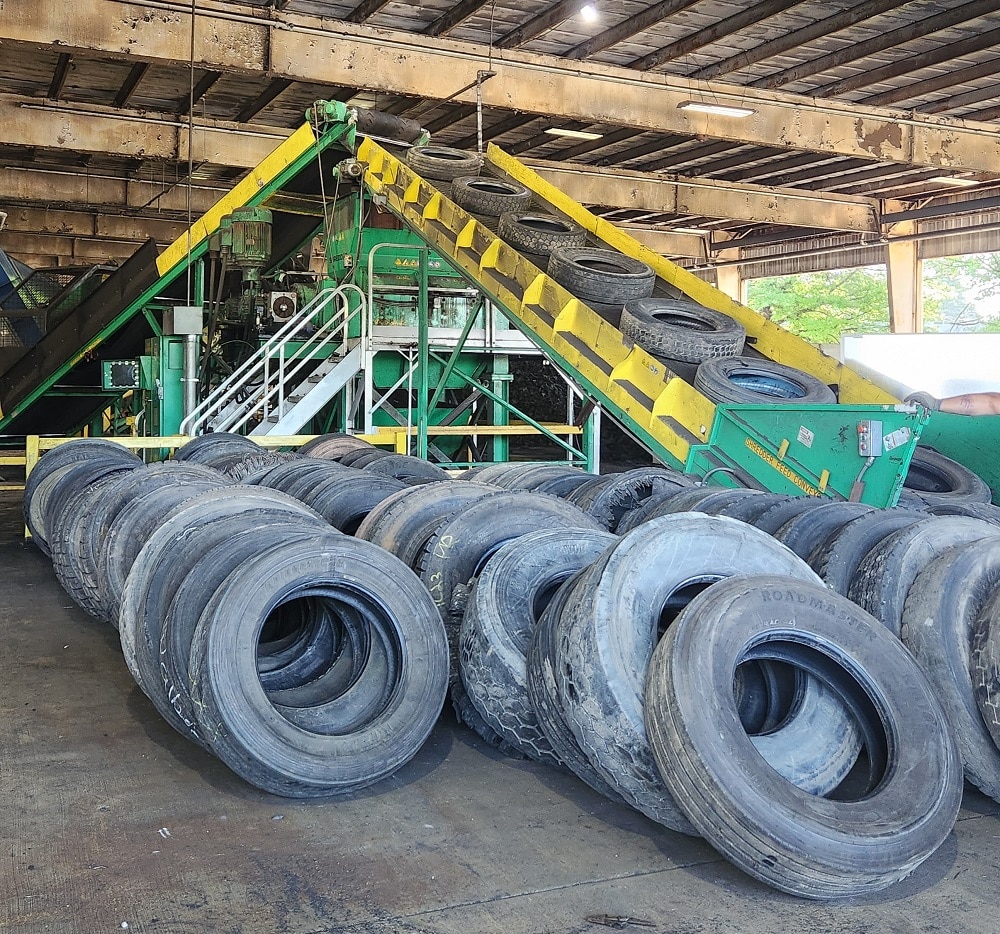
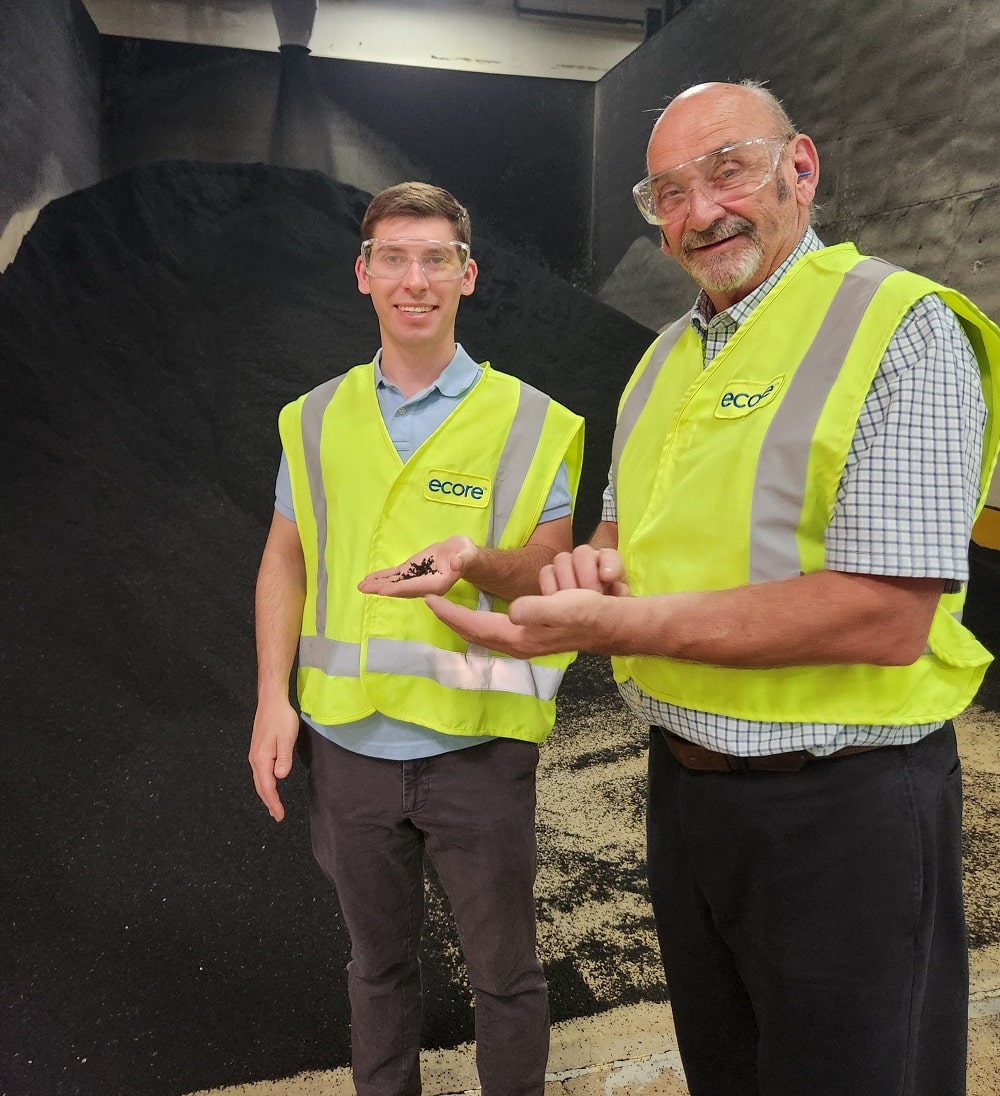
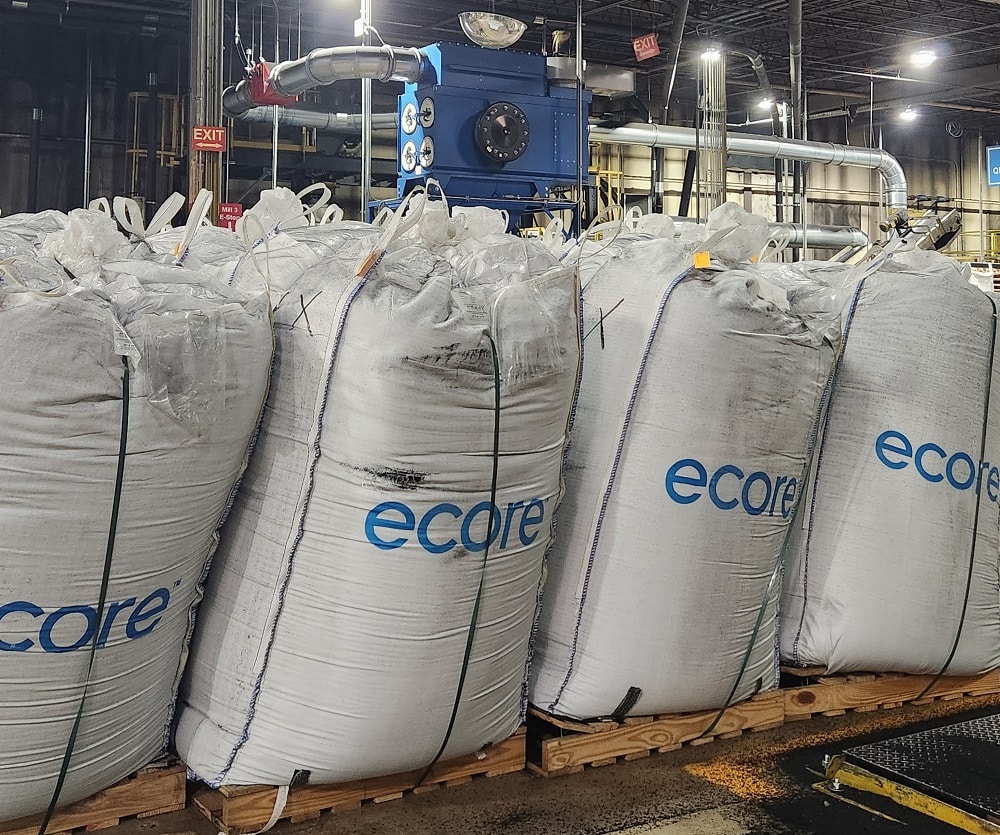
The production cycle (cylinder line) is comprised of 8 steps.
Mixing and pressing (the bagged materials)- Demolding
- Peeling
- Lamination
- Fusion bonding
- Rerolling
- Die cutting
- Automatic rerolling
In between the mixing & pressing and the demolding process MAGIC happens! The rubber is VULCANIZED! What does that mean?
Vulcanized rubber is rubber that has been treated through a process called vulcanization to improve its strength, durability, and elasticity. Ecore produces VCR (vulcanized composition rubber) that helps retain the natural performance benefits of rubber. Ecore starts with reclaimed rubber (diverted from landfills and incineration), transforms it into different-sized pellets, and then cures the material in a cylindrical roll.
The finished products are as unique as the process itself.
- Water Jet Logos to customize and brand any facility: https://www.ecoreintl.com/products/rubber/inlaid-rubber-logos
- Turf that simulates natural grass: https://www.ecoreintl.com/products/turf/fierceturf-monster
- Woven Vinyl that adds comfort under foot and acoustical control: https://www.ecoreintl.com/products/vinyl/woven-vinyl/ebb-flow-motivate
& of course, every type of rubber flooring known to man! Ecore controls their process to ensure flexibility and customization are available to brand facilities accurately.
TeamPAR is proudly utilizing Ecore rubber and vinyl flooring throughout the Lakeland Hills YMCA https://lakelandhillsymca.com/ where we are upgrading their entire fitness facility. Stay tuned for the transformation! Ecore is customizing their materials to bring performance and the YMCA culture together to tell the right story, with the right performance, at the right price, with the right ROI for lasting results for years to come.
Lean on TeamPAR and Ecore to elevate your facility…. We are ready to increase your ROI, together.